High resolution on the street requires high attention to production
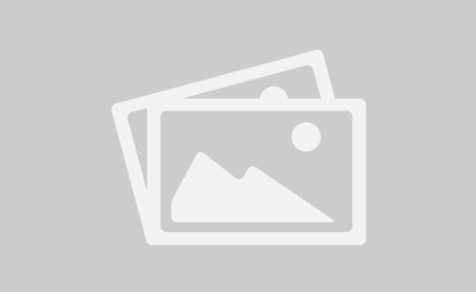
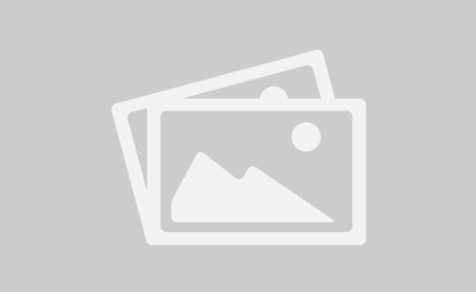
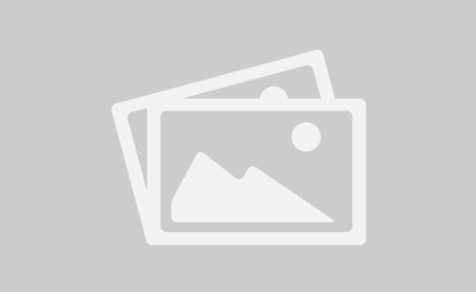
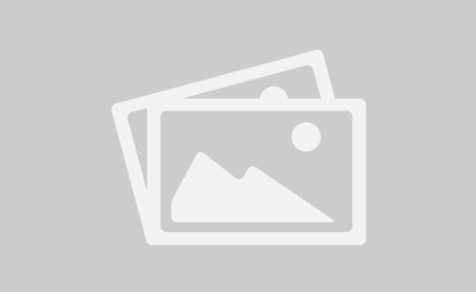
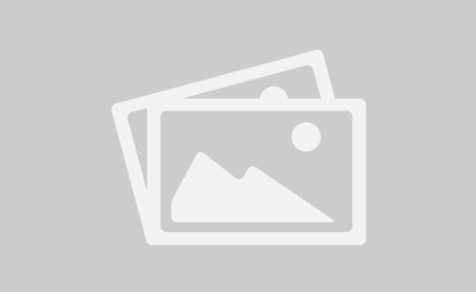
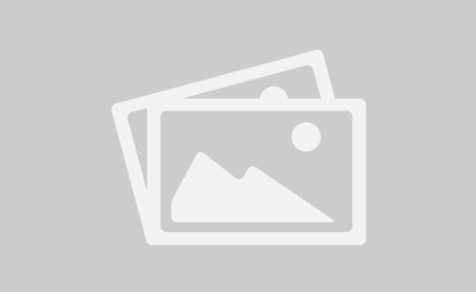
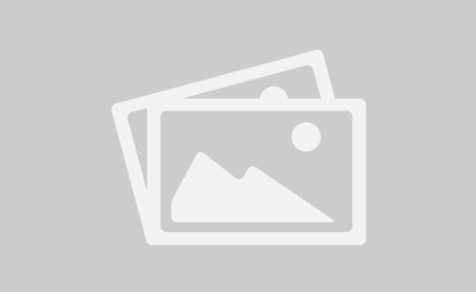
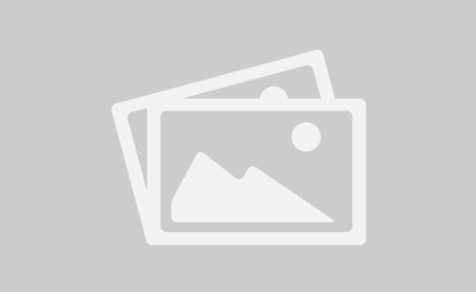
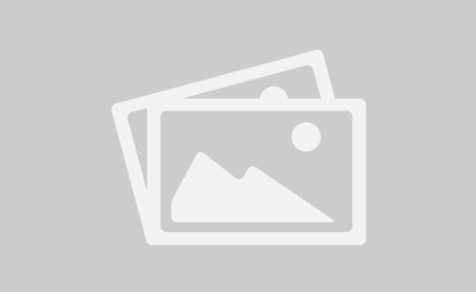
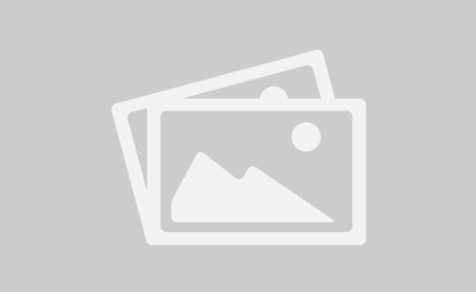
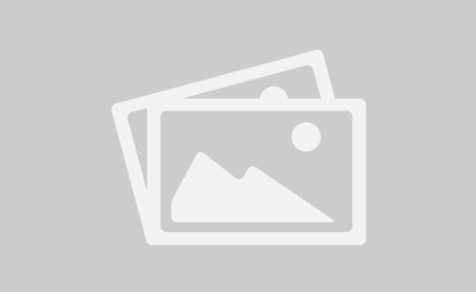
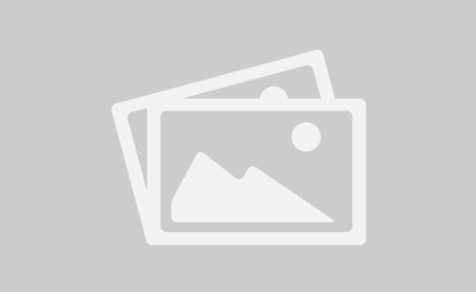
High resolution on the street requires high attention to production
It is really exciting to follow the rapid developments of High Definition headlights in the automotive lighting industry. Carmakers are seeking new ways to distinguish themselves. They embrace the application of high-resolution light modules in their headlights: for communication, comfort and safety.
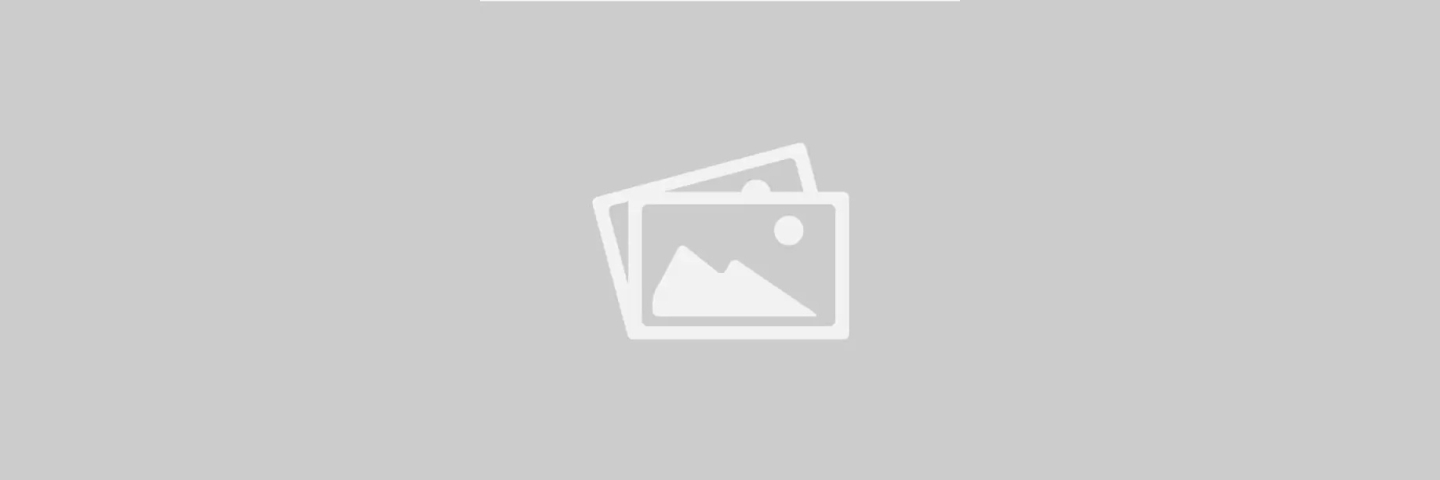
High Definition headlights add serious value to the carmaker, Tier 1 and car owner
Making projections on the street is of great assistance to the driver, as well as contributes to V2X communication. Tier 1’s love it because it adds serious value to their products. An important side effect is the reduction of the logistical efforts because HD headlamps can be equipped with dedicated software (for different global markets, the variety of different products like lift, right as well as legislation variations, will be drastically reduced).
Back to the Carmakers. Dedicated software is a great opportunity for personalization of the car, and has the potential to even open a new business model. The car owner can buy personalised software like projection of his name, or dynamic follow me home illumination.
Two parallel developments in new generation light modules
Two main streams are on top in HD projection: microLED and DMD. MicroLED is based on thousands of individually programmable LED’s, produced by e.g. Lumileds, Nichia, Osram. The Digital Micro-mirror Device (DMD) is based on up to 1.3 million (!) individually aimable micro-mirrors; basis is the Digital Light Processing Technology from Texas Instruments.
Production easier said than done
So we’re talking about where the light comes from. But then: how to get a detailed pattern of light beams on the road exactly where you want it to be? On one hand you need a set of high-quality projection lenses. On the other hand, you have to make sure that lenses and light source are extremely precisely assembled to each other. A slight deviation will ruin the outcome of your expensive light source and projection lenses!
Disruptive technology needed for HD light module production
Until recent, assembly of light modules often was based on straight forward assembly. No high-accuracy assembly was needed as tolerances were in the 0.1 mm range. For HD light modules however, a complete new way of assembly is necessary in order to have the optimal results (so pixels on the road were you want them to be). This new way is called Active Aligning, which allows fast assembly even with accuracies well below 5 micrometer (0.005 mm).
Active Aligning
In short, it means manoeuvring the lens-set in the (still liquid) glue, until you’ve have reached the optimal projected image. During the manoeuvring of the lens package, the light source is switched on, and at the same time the projection is automatically analyzed with high resolution cameras. In a number of steps (micro accurate movements of the lens-set to the light source or vice versa), the optimal image quality is determined. Once this is found, the glue cured (mostly by high speed UV curing). The result is an optimized light module which will keep its accuracy over its entire lifetime.
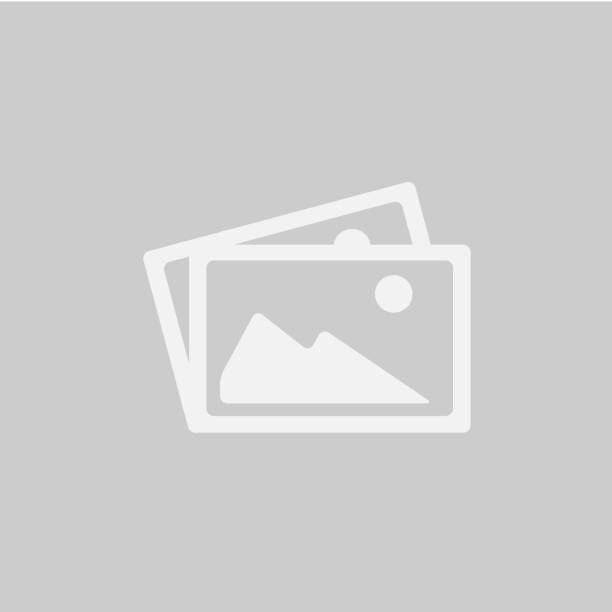
Let us advice you about micro separation
Are you looking for more information on automated separation of small parts? Get in touch and our experts will assist you with anything you need regarding automated manufacturing equipment. We are available by chat, email or by phone +31 546 805 580.
Let's create something groundbreaking together
Getting aligned: high performance at high speed
In the world of micro-optics and micro-structure assembly and testing, alignment is critical to achieve the desired performance.
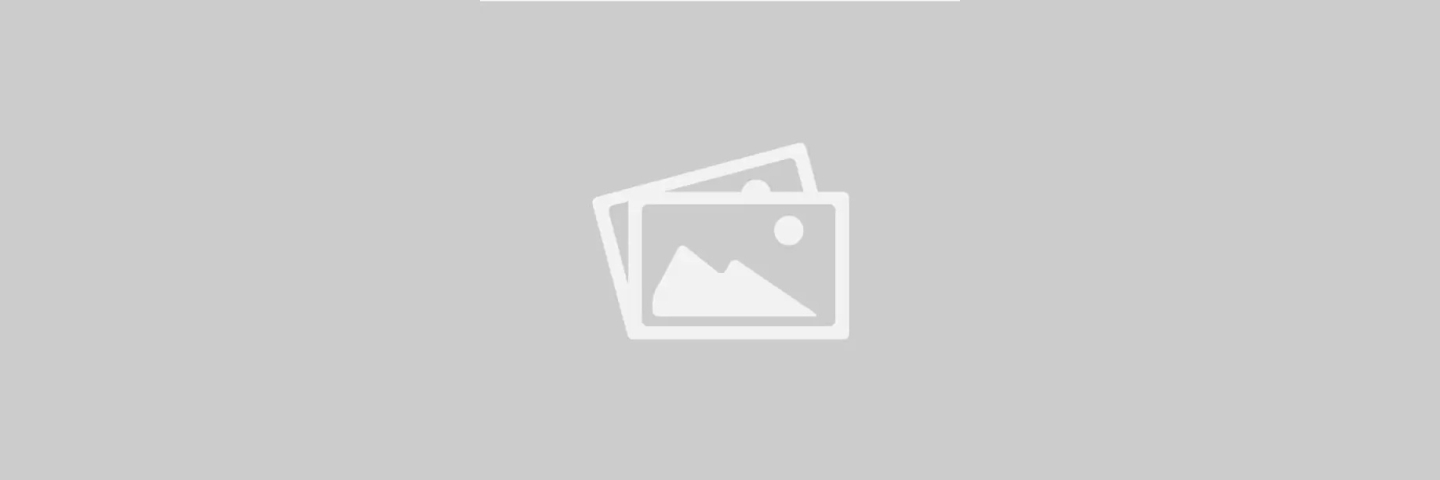
For more than 25 years, Integrated Mechanization Solutions in Almelo, more commonly known as IMS, has gained an expert position and a considerable track record in this field. IMS develops, builds, supplies, and supports high precision production systems ‘from lab to fab’. Over 130 professionals work with high precision to create test systems, operator workstations, stand-alone assembly systems, and fully automated production lines for customers worldwide.
High Precision
High precision assembly at IMS means small and complex products that need to be assembled with precision levels of a few- hundreds of millimeters down to one-tenth of a micron or even less. Examples of products that require such accuracy are automotive lighting systems and sensors, medical implants and surgery equipment, security systems and drone cameras, and many components in mobile phones and other smart devices.
Photo: Consumers, and therefore industries, are asking for higher performance, more complex, and smaller devices and sensors, which in turn increases the demand for high quality imaging. This drives up the accuracy of manufacturing optical systems. As complexity and accuracy increase, so do manufacturing challenges. Many optical system production systems can no longer rely on only mechanical alignment of components but need active alignment.
Assembly of Optics
A very specific class of products for which IMS builds production systems are micro-optics and camera modules. Keeping cost down while still achieving high performance requires more than just considering size and shape when we deal with optics. Here, we need to look at actual optical performance while putting components together – also known as active alignment. Whether lens-to-lens, lens-to-camera sensor, laser-to-lens, lens to-LED, and many more, these subassemblies require measuring optical performance using an image or projection while putting components together. Quite often this means that components need to be manipulated in 6 degrees of freedom while continuously measuring optical performance until an optimum configuration is reached.
Scalable Solutions
A major consideration in developing production systems at IMS is offering solutions than ‘grow’ with the customer’s challenge – both in volume as well as in product design. Especially in early stages of product development, design changes need to be handled. Also, very often a family of products need to be produced using the same or similar equipment. Furthermore, production volumes are expected to increase as the customer’s product becomes more successful, requiring a higher level of automation. IMS builds modular production systems from semi-automated, fully automated to unmanned, to handle these challenges.
Photo: Our production lines are scalable in capacity, capable of a high-mix and flexible in layout. When developing a production line, we’re making use of our standard automation platforms, which form a reliable and robust basis to integrate the needed manufacturing and assembly processes on.
Active Alignment System with Unique Features
IMS released a highly modular and scalable production system for optics assembly: GRASP OAS. GRASP OAS is a camera module assembly workstation fit to be used alike in R&D environments, small to medium volume production systems, and in highly automated production lines. Lens systems can be actively aligned to a camera sensor using the GRASP OAS with an accuracy of only 1 micron – a high accuracy that is needed to obtain the best camera module performance. Fast algorithms and controls provide quick feedback and short cycle times, which is needed for scaling up production volume. With only a limited number of modifications, the system can handle different types of optical systems, e.g. lidars.
The GRASP OAS can be equipped with different types of cleaning, dispense and curing systems in accordance with customer demands. Furthermore, and unique to the world of active alignment production systems, is a feature to freeze the alignment without fixating the components. This feature is called the Position Freezing Carrier: it holds the aligned optics and allows it to be fixated in a parallel step, next to the alignment station. This eliminates the need for pre-curing glues and reduces cycle time – hence saves costs. Additionally, it allows product developers to reconsider the fixation of components altogether, thus provides high design freedom.
Photo: The main steps of the Position Freezing Carrier (patented).
Scaling Up and Down
Active alignment is applied in many applications. Automotive head lights using more advanced (accurate) LED, laser, and lidar systems, require economic, scalable, and accurate active alignment solutions. Quality and performance of components are going up, enabling the automotive industry to meet increasing sustainability and safety demands and get ready for autonomous driving.
Another field of application of active alignment that is rapidly increasing is integrated photonics. Photonic integrated circuits (PICs or photonic chips) are now finding their ways into telecom, medical, computing, and many more applications rapidly. Allowing these PICs to communicate to other PICs or the ‘outside world’ using glass fibers or fiber arrays, rely on active alignment to guarantee the best coupling and minimal signal loss. Here IMS is working on production systems that make this possible – in other words: IMS is aligning for high performance at high speed.
Main steps of the Position Freezing Carrier (patented):
- After actively aligning the optics in six degrees of freedom, the ‘intermediate body’ that holds the optics is ‘frozen’, i.e. clamps are closed.
- It can now be moved into a parallel process, e.g. glue curing, while the Active Alignment workstation can continue with the next product.
- Once the bonding is completed, the parts return to the main production track.
- When the assembly is completed, parts are removed from the production line and the intermediate body is in its rest position.
Can your products and processes use more precision?
We are ready to assist you with a fitting solution. Take a look at our products or get in touch for more information. The possibilities of automation are endless at IMS.
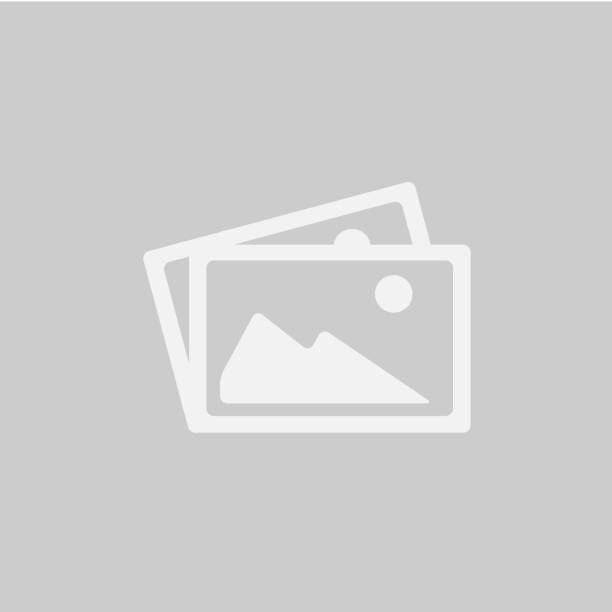
Let us advice you about micro separation
Are you looking for more information on automated separation of small parts? Get in touch and our experts will assist you with anything you need regarding automated manufacturing equipment. We are available by chat, email or by phone +31 546 805 580.
Let's create something groundbreaking together
When, Why and How to use Active Alignment?
Active Alignment: high quality assembly made easier and faster with lower total cost of ownership
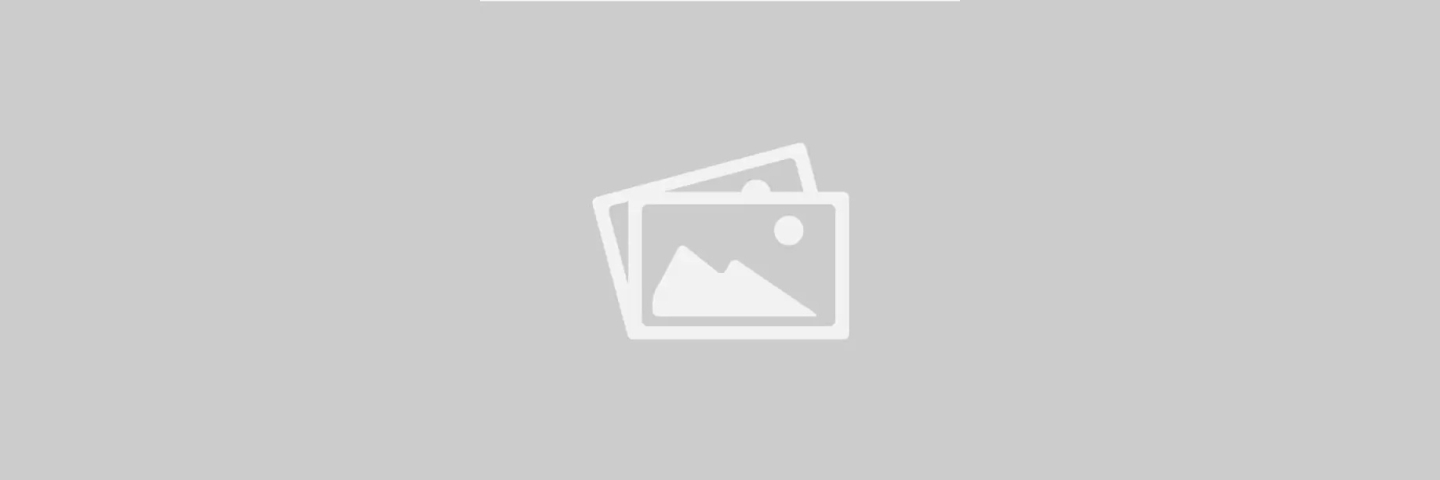
The major advantage of active alignment is achieving very high product performance. While individual components do not need to be extremely geometrically accurate. With the help of active alignment, the optics are placed in the best position according to the image -quality, -projection, or coupling power. Hence, the optical ‘loss penalty’ is very low. This way, higher yields can be achieved than compared to geometrical or mechanical alignment. Component costs can be reduced as these do not need excessive accuracy (e.g. accurate geometry of outer contours). Waste is also reduced.
1. Background / Ground for improvement
As a machine builder, we regularly talk to our customers and solve their issues. The challenges that our customers face are, amongst others:
- Standard equipment is not easily configured
- When not integrated, multiple suppliers are needed for one production line
- A large portion of the active alignment cycle is curing time, resulting in low utilization rate of an expensive manipulator
- Limited selection of glues for fast curing
- For higher volumes, the AA machine often needs to be duplicated instead of only the bottleneck
Furthermore, customers are looking for a system that can handle a product family or even products of different designs. They are in need of flexibility in production; and optimization towards total cost of ownership. If you are not sure about improvements that can be made, we offer a free pre-automation analysis to get started easily.
All this has resulted in our new -internally developed- IMS active alignment system with two key features: a modular ‘AA-workstation’ and an innovative way to split the alignment and bonding stages in the production process.
2. Modular Active Alignment workstation
The system is built as a module: it fits many different production system architectures and is capable of handling a large variety of products. The current version is built for assembling products such as camera systems, lens assemblies, LiDARs, automotive head lights and projector systems, and similar. Proprietary algorithms allow the system to align the components within several seconds. Also, orientation of assembly can easily be adjusted. The alignment can currently be done with an accuracy of 100 nanometers while steering on the optimal figure of merit (MTF, intensity, edge detection, encircled energy, etc.).
3. Major advantages of splitting alignment and fixation
What is probably most remarkable about the new IMS 6DOF-AA-workstation, is that it has the option of splitting the active alignment process step and the bonding step. Where most systems require the bonding (often UV curing glue) to take place inside the AA-workstation, IMS has invented a system whereby the bonding can take place in parallel. This saves precious time and maximizes the production of the AA-workstation, so in effect it is much more economic. It puts active alignment in a whole new perspective since it is made easier and faster with a lower cost of ownership!
Splitting the alignment and bonding step is done by using the ‘Position Freezing Carrier’ (IMS patent). After alignment in 6 degrees of freedom, it mechanically freezes the position of the two aligned components towards each other, currently with an accuracy of ±800 nanometers in focus direction. When the position is locked, the product directly goes into a parallel workstream for bonding. The alignment workstation is than already loaded with the next product. This means that the utilization rate of the AA workstation is much higher thus more economic. No need to wait for the first curing step and elimination of this alignment error (glue shrinkage).
Additionally, the position freezing carrier may challenge you to re-think your bonding strategy by offering more product design freedom. Overall bonding is no longer the bottle neck of the process so why not consider to take out the fast cure? Furthermore, new assembly options become available now. For example, you may no longer need an oven for glue curing.
New Active Alignment possibilities in automotive-, medical and photonics!
Active alignment is ready for its next generation. IMS, located in Almelo, the Netherlands, reinvented the technology and transformed it into a modular system to meet future needs of the automotive-, medical– and photonics market. On top of that, the exiting novelty of the Position Freezing Carrier boosts the output and quality level even more. A video about the active alignment solution can be found on YouTube.
Interested to know more about how our automated assembly lines can help your company?
IMS is your partner in enhancing your production capabilities. Do you want to know more about production automation or do you have a specific automation challenge for your innovative product? Get in touch! We are happy to assist you further!
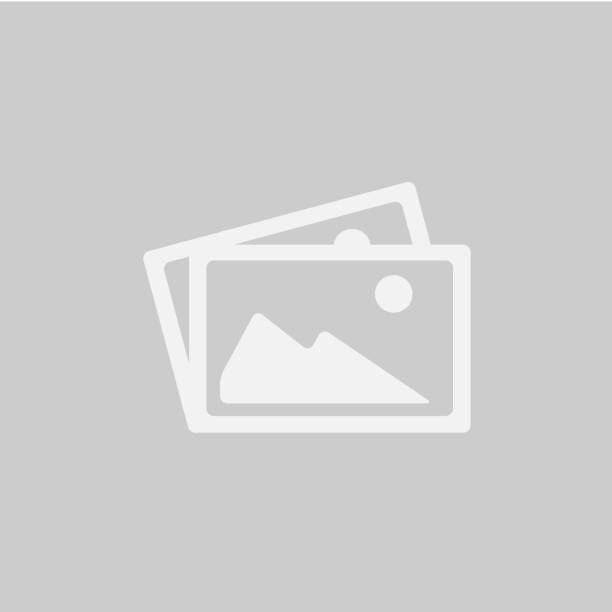
Let us advice you about micro separation
Are you looking for more information on automated separation of small parts? Get in touch and our experts will assist you with anything you need regarding automated manufacturing equipment. We are available by chat, email or by phone +31 546 805 580.
Let's create something groundbreaking together
Wire cutting with laser
It’s a real challenge to find the best custom production solution there is for something that’s quite broad. There are so many factors and parameters to take into account here.
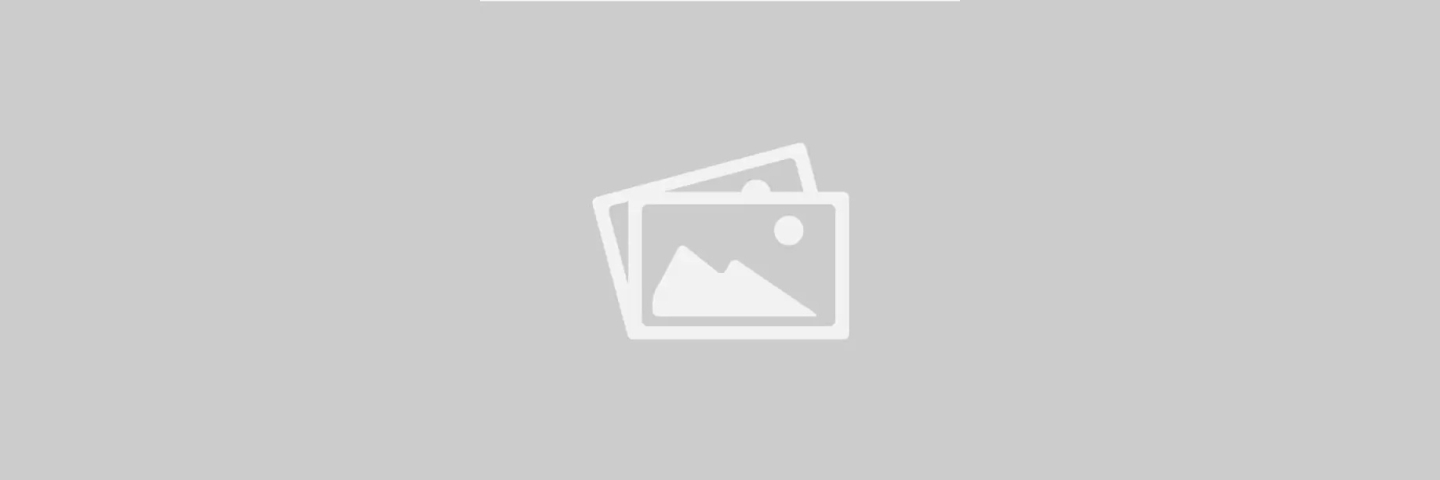
Especially when customer processes are not optimal yet. This client asked us to find the best possible method to cut very small and thin wires. The cuts should be extremely consistent and accurate. These precise cuts guarantee product quality. And with length tolerances of 20 micron and position tolerances of 50 micron we surely succeeded in this project.
Technological highlights for reliability
We always thrive on the best possible outcome. It’s often by means of quality and output that we’re taking customers steps ahead. To get a good view of the cutting processes first, we performed a benchmark for this. This benchmark makes it possible to think outside the box.
We position the wire by means of mechanical alignment. Our customer requires perpendicular and very reliable cuts. This requirement brings us to looking at different cutting techniques. The one that came out as a winner was laser cutting. Laser cutting does not have tool wear, and the cuts perfectly aligned with the required processes. We obtain the best results here with a Femtosecond USP laser.
For fixating we used a needle adhesive dispensing system with fast UV curing. Our machines are always built to generate maximum output with the best possible quality. This resulted in a cycle time of 2.4 seconds per product. And we integrated 100% inline inspection of value added processes.
Application specific benefits
High precision automation in production enables fast and reliable results. As it’s the best solution to a problem that can’t be solved by human hands. Even with the correct tools, automated precision machines are more accurate and reliable than operators. The application of the laser wire cutter offers a reel-to-reel application. The wire gets unloaded and reloaded back on another reel. The machine is stable and highly repeatable when it comes to cutting quality. And as stated before, with a cycle time of only 2.4 seconds, it’s very fast.
Looking to produce exact cuts for your product as well? We’re right beside you
We’re right here when you’re facing high precision cutting challenges. Our engineers offer solutions that are not thought of before. This way of thinking takes your production environment steps ahead. Get in touch for more information.
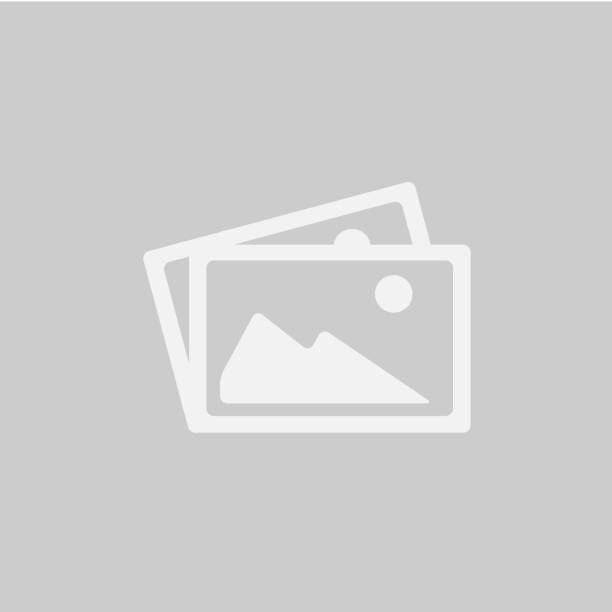
Let us advice you about micro separation
Are you looking for more information on automated separation of small parts? Get in touch and our experts will assist you with anything you need regarding automated manufacturing equipment. We are available by chat, email or by phone +31 546 805 580.
Let's create something groundbreaking together
Separation of very small parts
Finding and integrating precision production automation methods for accurate separation of tiny parts from pre-formed multi-layered metal sheets, inspection and packaging.
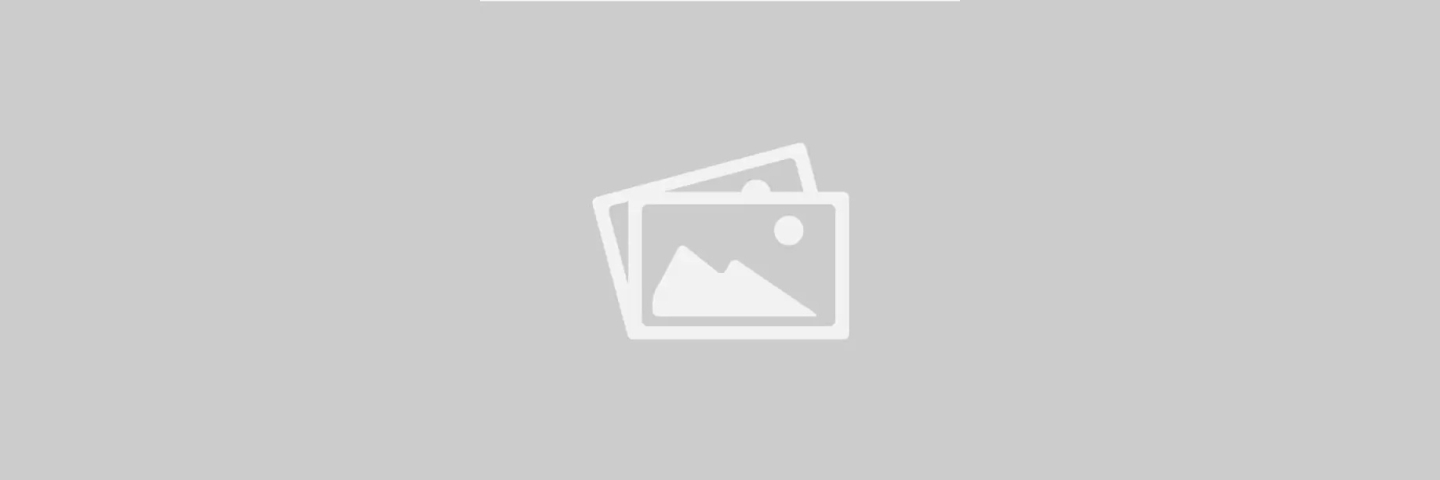
In precision manufacturing, technology plays a large role. Particularly in industries working with tiny parts, a precision machine for separating these parts has taken center stage. This machine has enhanced processes, providing unparalleled precision and speed. It brings a variety of application advantages that elevate manufacturing standards.
Technological Highlights
Pre-measurement of actual product position
Imagine a process where the machine already knows the exact position of each minuscule part before it even begins. This is the power of pre-measurement. Pre-measurement is a feature that ensures every cut has incredible precision.
Mechanical alignment positioning
With mechanical alignment positioning, these machines achieves alignment perfection. The high precision machines do not leave any room for error and ensure an exact separation every time.
Benchmarking cutting processes
By benchmarking cutting processes, manufacturers can fine-tune their operations for high quality, maximizing productivity and minimizing waste.
Selected process: mechanical separation
Mechanical separation is the chosen process for this machine. Its reliability, combined with the intricate mechanisms of precision machines, guarantees consistent outcomes.
6-Second cycle time
Time is money, and automation machines work on this philosophy. With an impressive 6-second cycle time, these machines can process a large number of parts in a remarkably short period. Enhancing overall production.
Packaging to industrial standard gel tray
The process does not stop at separation. The integrated process packages the separated parts into industrial-standard gel trays. Our machines streamline the packaging process and maintain the same level of accuracy.
100% Inspection
Flawlessness is non-negotiable. Our machines come equipped with a 100% inspection feature, leaving no room for defects. It inspects every part before packaging. Ensuring the highest quality for the market.
Application Benefits
Metal sheet to packaging in gel tray
Whether it’s delicate electronic components or intricate metal parts. Our machines are versatile enough to handle all sorts of materials, ensuring that they reach the final destination.
Stable and repeatable separation of precision parts
Inconsistent cuts can lead to many problems downstream. The machine stability of separating parts enables seamless downstream operations and assembly.
Short cycle time
Efficiency shines once more with the short cycle time. By reducing processing time without compromising accuracy, manufacturers witness a surge in overall productivity, subsequently boosting their competitive edge.
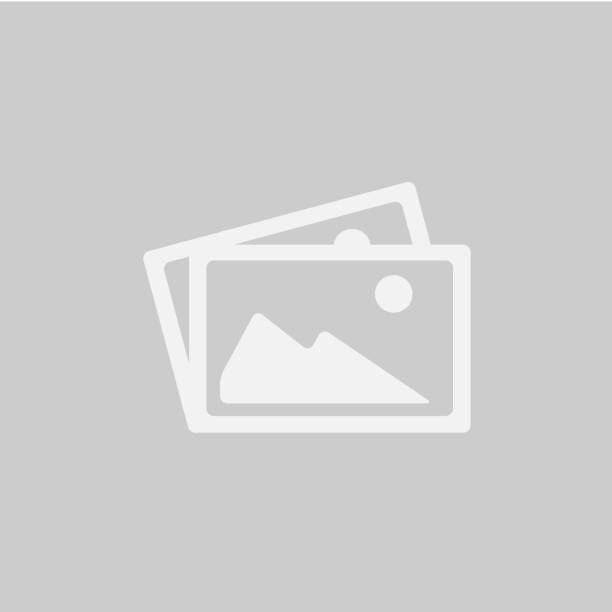
Let us advice you about micro separation
Are you looking for more information on automated separation of small parts? Get in touch and our experts will assist you with anything you need regarding automated manufacturing equipment. We are available by chat, email or by phone +31 546 805 580.
Let's create something groundbreaking together
Surface inspection by deep learning
Finding and implementing optimum automated product surface inspection technology, which is more accurate, repeatable and consistent than human quality inspection, while maintaining flexible to product variation and future adaptability.
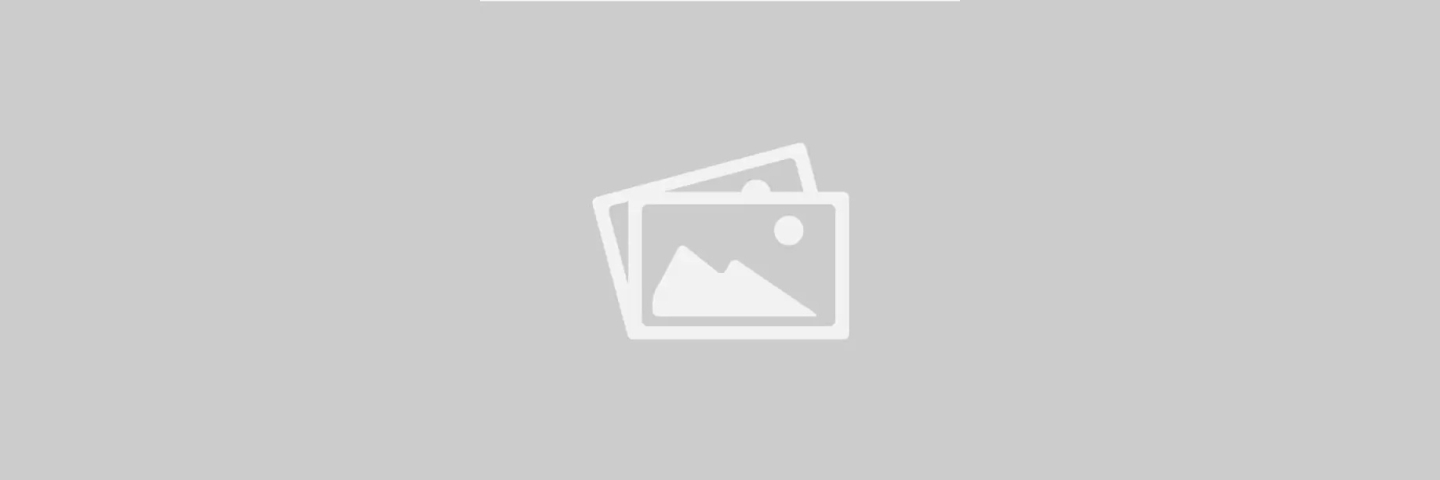
Technology highlights
- Medical Product
- Automated optical inspection of various surfaces
- 100% in-line inspection
- Optical system for 3D inspection, including rotation of product
- Deep learning algorithms used for qualification
- Searching for defects: damage, burrs, dents, scratches, color differences, burning effects
- User can easily access and program system for a wide range of recipes for combining camera inputs, deep learning and quality criteria
Application specific benefits
- Algorithms use Deep Learning Technology
- Training of known and unknown product defects (supervised/unsupervised)
- Wide range of product portfolio (>1000 product types possible)
- Replaces inspection by humans: more reproducible
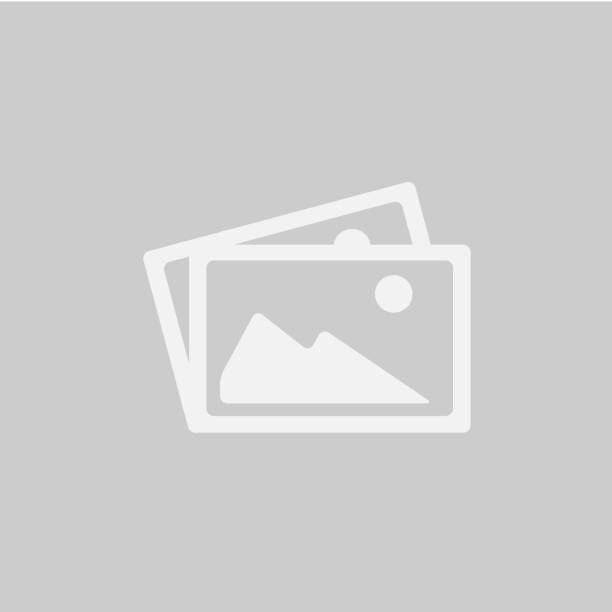
Let us advice you about surface inspection
Are you looking for ways to add automated surface inspection to your manufacturing processes? We are looking forward to help and advice you to come to the best solutions for your products. Get in touch through our contact form, send us an email or start a chat.