Reducing the footprint of cars worldwide
Reducing the footprint of cars can happen on a very small scale. It’s goals like this that make our work very diverse. This customer operates in a fast growing market.
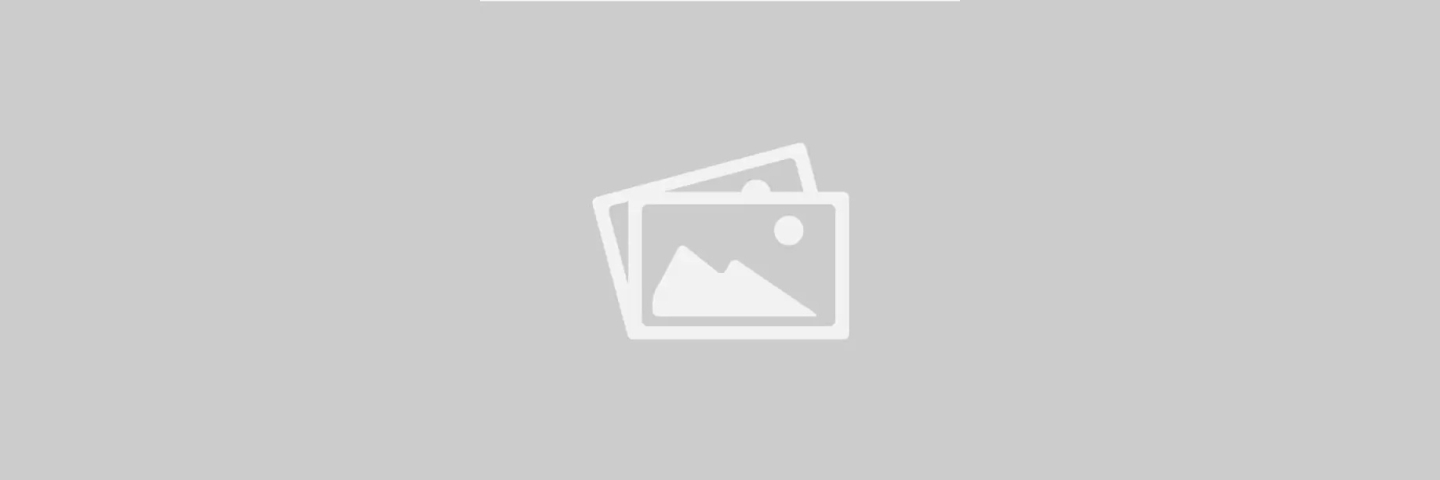
The growth is caused by European laws and regulations to reduce exhaust emissions. This case involves automation for the precise assembly of a small micro-dosing system. The system doses additives that supports the reduction of exhaust emission.
Finding new solutions to specific challenges
The customer likes its production capacity to match the market demands. They requested the use of existing manufacturing processes and asked us to find solutions for a number of additional process steps. The resulting production line should be robust, reliable and easy to operate.
DFA and DFM
Before taking on the challenge, we conducted a pre-automation analysis to get a good view of the assembly line. Besides the integration of new processes, we needed to integrate and validate existing supplier processes as well. The pre-automation analysis was conducted together with the customer. This led to a much better producibility of the product. Our engineers made use of the Design For Assembly (DFA) and Design For Manufacturing (DFM) methodology.
The new production line enables the customer to produce over 2,000,000 micro-dosing systems per year. These systems are manufactured at 10 seconds per product cycle time. The basis of this production line is formed by a standardized automation platform.
The following processes were integrated into the production line:
- Laser welding;
- Vision check;
- Height measurement;
- Pressure testing;
- Water test;
- Flow testing;
- Encoding.
Running on a tight schedule
The project had to be realized in a relatively short amount of time. We proposed a tight, but realistic planning to answer this question. Due to the growing demand of this product, the customer asked us if it was possible to speed up the process. The faster process required joint efforts of ourselves and the customer. We managed to find a solution for this and shortened the delivery time by six weeks. This enabled the customer to meet demands earlier than expected.
Due to the flexibility on both sides, we managed to finish the project with a successful Factory Acceptance Test (FAT) and Site Acceptance Test (SAT). The customer is satisfied with the fast delivery and employment of the machine. As the machine has proven itself over time, there are now more than five copies on location.
Flexible solutions for increased production capacity
The project results in a flexible and precise production solution. The production line is very scalable and proofs itself every time. The concrete benefits for the customer are:
- Meeting market demands earlier than expected;
- Further increase of production capacity;
- Flexible solution to scale up when necessary;
- Stable production processes.
Need help with Design For Assembly or Design For Manufacturing?
We get involved into your production challenges early to make a big impact. Get in touch with us for advice on your production systems.
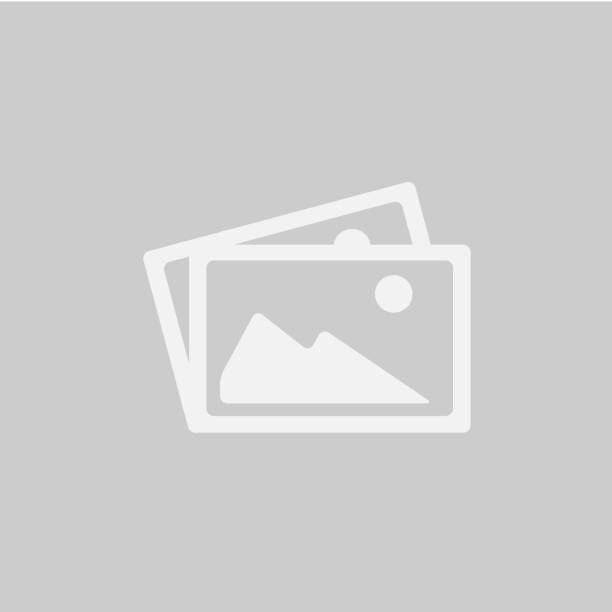
Let us advice you about reducing the footprint of your production
Are you looking for more information on reducing the footprint of your production? Get in touch and our experts will assist you with anything you need regarding reducing the footprint of your production lines. We are available by chat, email or by phone +31 546 805 580.