High resolution on the street requires high attention to production
It is really exciting to follow the rapid developments of High Definition headlights in the automotive lighting industry. Carmakers are seeking new ways to distinguish themselves. They embrace the application of high-resolution light modules in their headlights: for communication, comfort and safety.
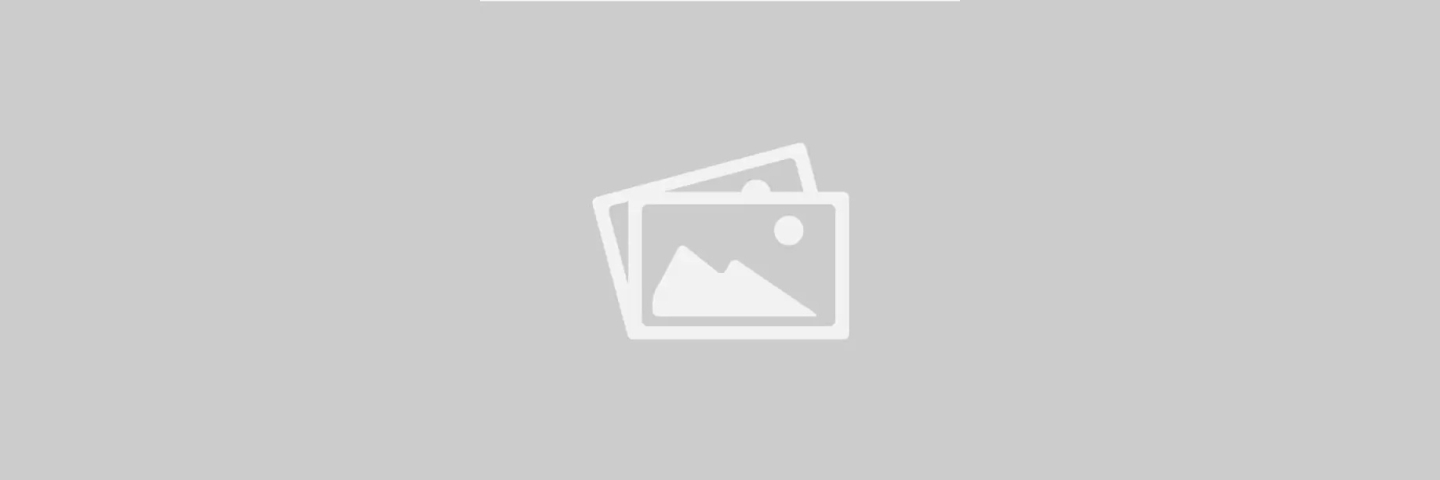
High Definition headlights add serious value to the carmaker, Tier 1 and car owner
Making projections on the street is of great assistance to the driver, as well as contributes to V2X communication. Tier 1’s love it because it adds serious value to their products. An important side effect is the reduction of the logistical efforts because HD headlamps can be equipped with dedicated software (for different global markets, the variety of different products like lift, right as well as legislation variations, will be drastically reduced).
Back to the Carmakers. Dedicated software is a great opportunity for personalization of the car, and has the potential to even open a new business model. The car owner can buy personalised software like projection of his name, or dynamic follow me home illumination.
Two parallel developments in new generation light modules
Two main streams are on top in HD projection: microLED and DMD. MicroLED is based on thousands of individually programmable LED’s, produced by e.g. Lumileds, Nichia, Osram. The Digital Micro-mirror Device (DMD) is based on up to 1.3 million (!) individually aimable micro-mirrors; basis is the Digital Light Processing Technology from Texas Instruments.
Production easier said than done
So we’re talking about where the light comes from. But then: how to get a detailed pattern of light beams on the road exactly where you want it to be? On one hand you need a set of high-quality projection lenses. On the other hand, you have to make sure that lenses and light source are extremely precisely assembled to each other. A slight deviation will ruin the outcome of your expensive light source and projection lenses!
Disruptive technology needed for HD light module production
Until recent, assembly of light modules often was based on straight forward assembly. No high-accuracy assembly was needed as tolerances were in the 0.1 mm range. For HD light modules however, a complete new way of assembly is necessary in order to have the optimal results (so pixels on the road were you want them to be). This new way is called Active Aligning, which allows fast assembly even with accuracies well below 5 micrometer (0.005 mm).
Active Aligning
In short, it means manoeuvring the lens-set in the (still liquid) glue, until you’ve have reached the optimal projected image. During the manoeuvring of the lens package, the light source is switched on, and at the same time the projection is automatically analyzed with high resolution cameras. In a number of steps (micro accurate movements of the lens-set to the light source or vice versa), the optimal image quality is determined. Once this is found, the glue cured (mostly by high speed UV curing). The result is an optimized light module which will keep its accuracy over its entire lifetime.
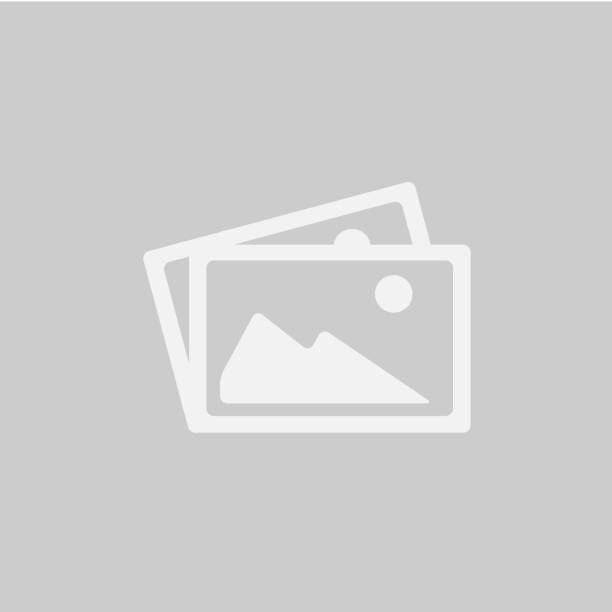
Let us advice you about micro separation
Are you looking for more information on automated separation of small parts? Get in touch and our experts will assist you with anything you need regarding automated manufacturing equipment. We are available by chat, email or by phone +31 546 805 580.