When, Why and How to use Active Alignment?
Active Alignment: high quality assembly made easier and faster with lower total cost of ownership
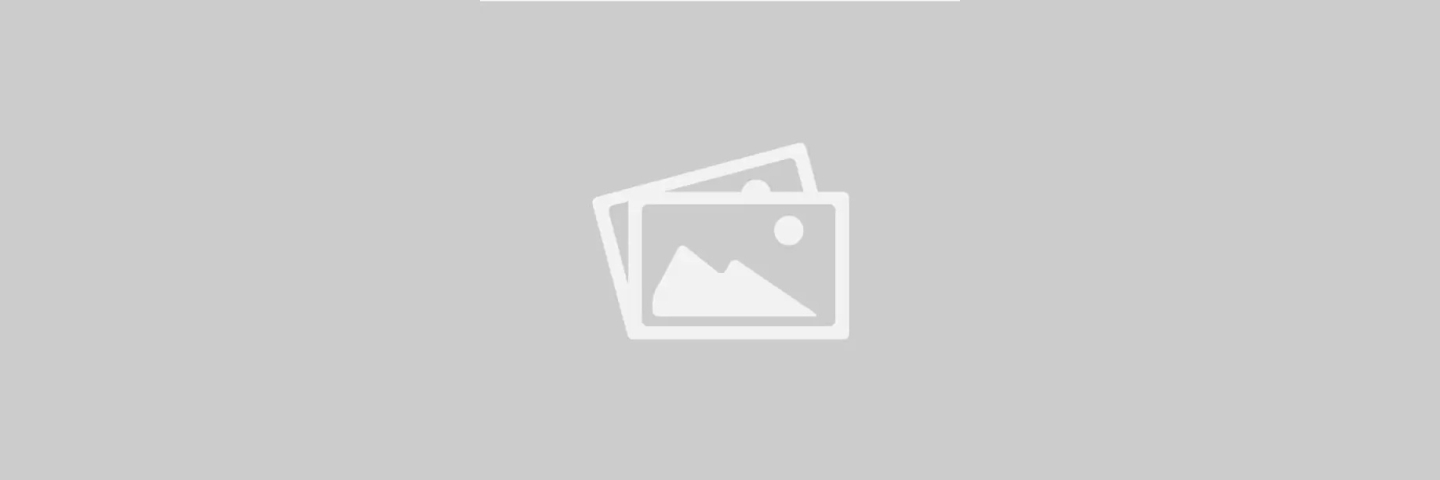
The major advantage of active alignment is achieving very high product performance. While individual components do not need to be extremely geometrically accurate. With the help of active alignment, the optics are placed in the best position according to the image -quality, -projection, or coupling power. Hence, the optical ‘loss penalty’ is very low. This way, higher yields can be achieved than compared to geometrical or mechanical alignment. Component costs can be reduced as these do not need excessive accuracy (e.g. accurate geometry of outer contours). Waste is also reduced.
1. Background / Ground for improvement
As a machine builder, we regularly talk to our customers and solve their issues. The challenges that our customers face are, amongst others:
- Standard equipment is not easily configured
- When not integrated, multiple suppliers are needed for one production line
- A large portion of the active alignment cycle is curing time, resulting in low utilization rate of an expensive manipulator
- Limited selection of glues for fast curing
- For higher volumes, the AA machine often needs to be duplicated instead of only the bottleneck
Furthermore, customers are looking for a system that can handle a product family or even products of different designs. They are in need of flexibility in production; and optimization towards total cost of ownership. If you are not sure about improvements that can be made, we offer a free pre-automation analysis to get started easily.
All this has resulted in our new -internally developed- IMS active alignment system with two key features: a modular ‘AA-workstation’ and an innovative way to split the alignment and bonding stages in the production process.
2. Modular Active Alignment workstation
The system is built as a module: it fits many different production system architectures and is capable of handling a large variety of products. The current version is built for assembling products such as camera systems, lens assemblies, LiDARs, automotive head lights and projector systems, and similar. Proprietary algorithms allow the system to align the components within several seconds. Also, orientation of assembly can easily be adjusted. The alignment can currently be done with an accuracy of 100 nanometers while steering on the optimal figure of merit (MTF, intensity, edge detection, encircled energy, etc.).
3. Major advantages of splitting alignment and fixation
What is probably most remarkable about the new IMS 6DOF-AA-workstation, is that it has the option of splitting the active alignment process step and the bonding step. Where most systems require the bonding (often UV curing glue) to take place inside the AA-workstation, IMS has invented a system whereby the bonding can take place in parallel. This saves precious time and maximizes the production of the AA-workstation, so in effect it is much more economic. It puts active alignment in a whole new perspective since it is made easier and faster with a lower cost of ownership!
Splitting the alignment and bonding step is done by using the ‘Position Freezing Carrier’ (IMS patent). After alignment in 6 degrees of freedom, it mechanically freezes the position of the two aligned components towards each other, currently with an accuracy of ±800 nanometers in focus direction. When the position is locked, the product directly goes into a parallel workstream for bonding. The alignment workstation is than already loaded with the next product. This means that the utilization rate of the AA workstation is much higher thus more economic. No need to wait for the first curing step and elimination of this alignment error (glue shrinkage).
Additionally, the position freezing carrier may challenge you to re-think your bonding strategy by offering more product design freedom. Overall bonding is no longer the bottle neck of the process so why not consider to take out the fast cure? Furthermore, new assembly options become available now. For example, you may no longer need an oven for glue curing.
New Active Alignment possibilities in automotive-, medical and photonics!
Active alignment is ready for its next generation. IMS, located in Almelo, the Netherlands, reinvented the technology and transformed it into a modular system to meet future needs of the automotive-, medical– and photonics market. On top of that, the exiting novelty of the Position Freezing Carrier boosts the output and quality level even more. A video about the active alignment solution can be found on YouTube.
Interested to know more about how our automated assembly lines can help your company?
IMS is your partner in enhancing your production capabilities. Do you want to know more about production automation or do you have a specific automation challenge for your innovative product? Get in touch! We are happy to assist you further!
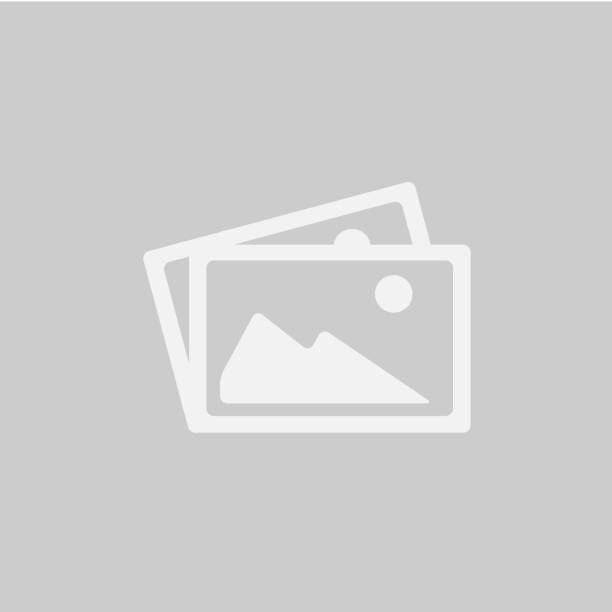
Let us advice you about micro separation
Are you looking for more information on automated separation of small parts? Get in touch and our experts will assist you with anything you need regarding automated manufacturing equipment. We are available by chat, email or by phone +31 546 805 580.